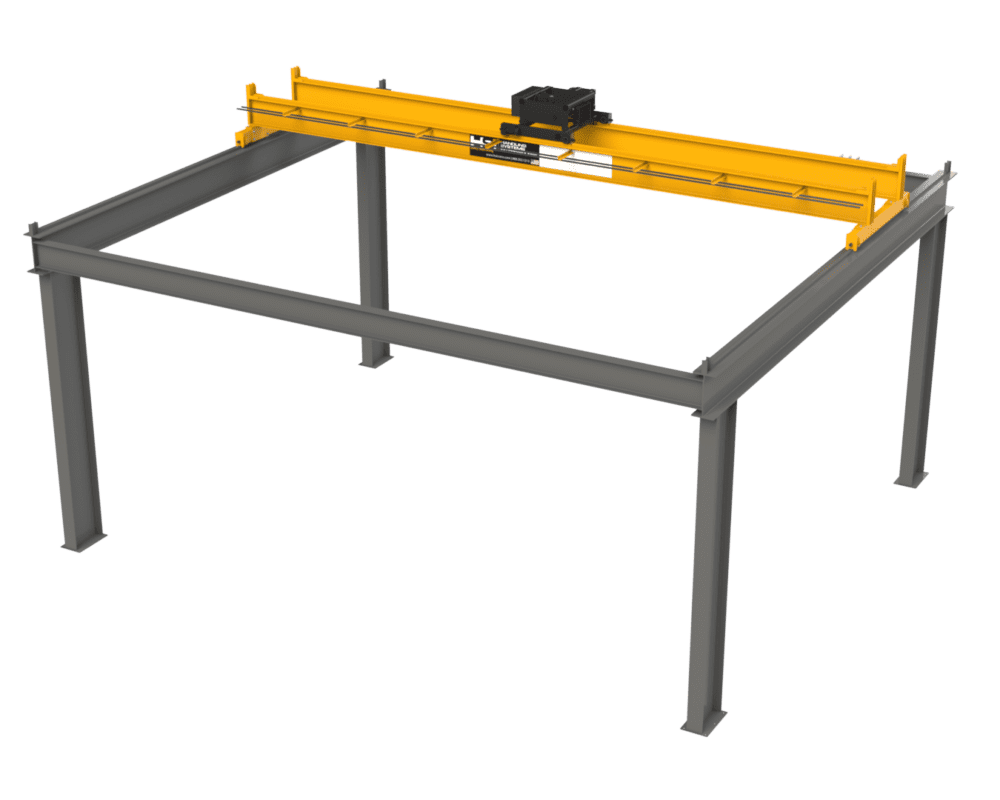
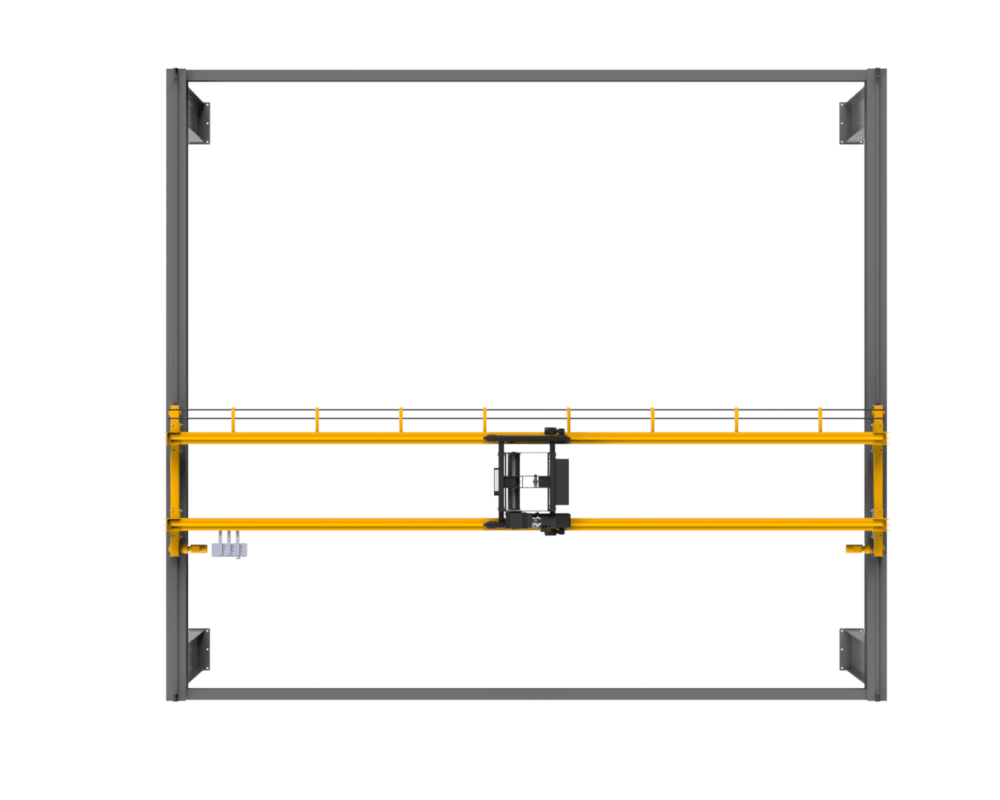
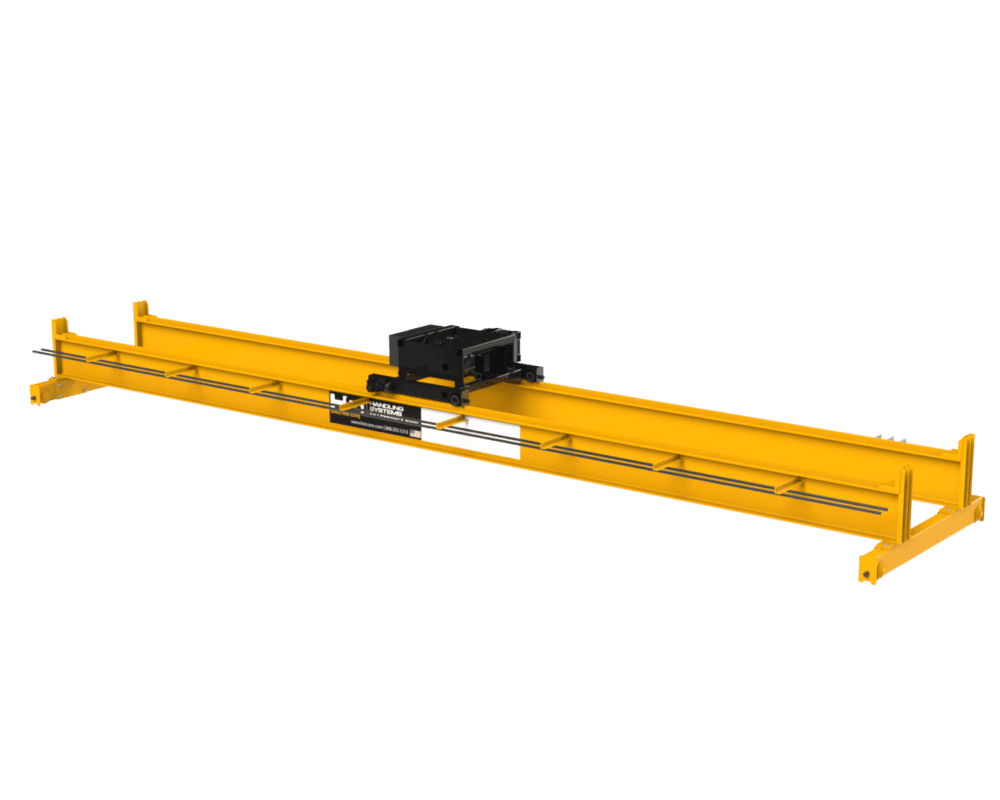
Double Girder Bridge Cranes
Girders serve as robust structural elements commonly employed in large-scale projects like bridges, buildings, and tunnels. Their unique design allows them to provide horizontal support while effectively handling both dynamic and static loads. This makes them equally valuable in heavy-duty lifting applications, including girder cranes.
Two prevalent types of cranes used for heavy material lifting are the single-girder and double-girder variants. Both fall under the category of overhead, or more specifically, bridge cranes, which feature horizontal runways and a mobile bridge equipped with a hoist. These cranes offer swift operation and often come with remote control systems for ease of use. In single-girder cranes, the hoist moves along a singular girder, while in double-girder cranes, the hoist travels between two parallel girders.
Each type presents distinct advantages in terms of lift and height capabilities. With single-girder cranes, the hoist hook is mounted below the girder and the assembly is affixed to its underside, reducing the vertical lifting range by 18 to 36 inches. Conversely, in double-girder cranes, the hoist operates in alignment with the girders, and its assembly is mounted atop them, allowing for greater lift heights for taller loads.
While both single and double-girder cranes are robust and durable, the latter is often favored for extremely heavy-duty and severe-duty tasks, also classified as D+ and E-rated lifting operations. This preference isn’t necessarily because double-girder cranes possess greater power or duty ratings, but rather because they typically come with more specialized features. These cranes are also more conducive to incorporating a service platform, offering technicians easier access for maintenance and service tasks.
Double-Girder Crane Offerings and Features:
Here at HIS Crane, we excel in crafting durable, high-performance cranes tailored to various applications and load capacities. Our cranes prioritize operator safety and are built to exceed the rigorous industry standards set forth by the Crane Manufacturers Association of America (CMAA). Our lineup includes three notable categories:
Top-Running Double-Girder Cranes
Our top-running models come in an array of lifting capacities to perfectly match your project requirements. Options range from 3-ton to 5-ton, 7.5-ton, and even up to 20 tons, with all featuring fixed-axle wheels for added stability.
Class D Double-Girder Cranes
These cranes are fully compliant with, or surpass, CMAA Class D standards and are capable of handling loads up to 60 tons. Depending on the weight rating, these cranes come equipped with rotating axle wheels; cranes designed for 40 tons or less feature four wheels, while those rated for over 40 tons come with eight wheels for added durability and stability.
Custom Crane Solutions
We specialize in custom-designed cranes tailored to meet your project’s unique specifications, even for carrying capacities of up to 1,000 tons. Our engineers craft highly specialized lifting equipment that is suitable for extreme industrial applications, such as aerospace, military operations, and nuclear fuel facilities. Our tailor-made cranes can be configured with multiple girders and are designed to meet heavy-duty lifting requirements, adhering to CMAA Classes A-F.
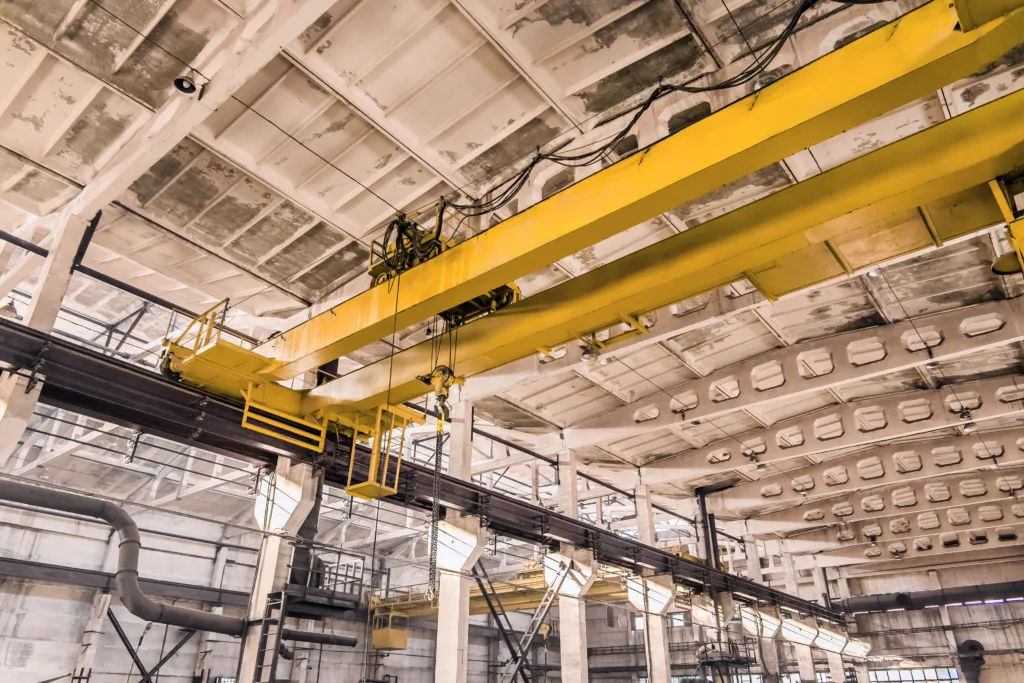
Additional Info
Girders serve as robust structural elements commonly employed in large-scale projects like bridges, buildings, and tunnels. Their unique design allows them to provide horizontal support while effectively handling both dynamic and static loads. This makes them equally valuable in heavy-duty lifting applications, including girder cranes.
Two prevalent types of cranes used for heavy material lifting are the single-girder and double-girder variants. Both fall under the category of overhead, or more specifically, bridge cranes, which feature horizontal runways and a mobile bridge equipped with a hoist. These cranes offer swift operation and often come with remote control systems for ease of use. In single-girder cranes, the hoist moves along a singular girder, while in double-girder cranes, the hoist travels between two parallel girders.
Each type presents distinct advantages in terms of lift and height capabilities. With single-girder cranes, the hoist hook is mounted below the girder and the assembly is affixed to its underside, reducing the vertical lifting range by 18 to 36 inches. Conversely, in double-girder cranes, the hoist operates in alignment with the girders, and its assembly is mounted atop them, allowing for greater lift heights for taller loads.
While both single and double-girder cranes are robust and durable, the latter is often favored for extremely heavy-duty and severe-duty tasks, also classified as D+ and E-rated lifting operations. This preference isn’t necessarily because double-girder cranes possess greater power or duty ratings, but rather because they typically come with more specialized features. These cranes are also more conducive to incorporating a service platform, offering technicians easier access for maintenance and service tasks.
11 Year Warranty
HSI’s 11 year warranty is the best in the industry.
What Products Are Covered?
• Manual Rotation Jib Cranes
• Manual Steel Gantry Cranes
• Defects in material and workmanship
The Fine Print:
Handling Systems International, Inc. (known as H.S.I.) warrants manual push/pull Jib and Gantry Crane products it manufactures against defects in material or workmanship for a period of eleven years from date of receipt by purchaser or customer. This warranty does not cover failure or defect in paint or material finish. This warranty does not cover failure or defect caused by operation in excess of recommended rated capacities, misuses, negligence or accident, and alteration or repair of any kind not authorized by H.S.I. H.S.I. systems shall not be modified after manufacture without written authorization of H.S.I. Any field modifications made without written authorization of H.S.I. shall void all H.S.I.’s warranty obligation. H.S.I. agrees to furnish the same or substantially similar replacement part (new or repaired) free of charge, providing the buyer gives immediate written notice of alleged defects, and if requested by H.S.I., returns the defective parts to the factory, for H.S.I.’s inspection and examination. Purchaser or end user shall be solely responsible for all freight and transportation costs incurred in connection with any warranty work provided by H.S.I. hereunder. H.S.I. will not be liable for any loss, injury or damage to persons or property, nor for damages of any kind resulting from failure or defective operation of any materials or equipment furnished hereunder. H.S.I. shall not be liable under any circumstances for any incidental, special and/or consequential damages whatsoever, whether or not foreseeable, including but not limited to damages for lost profits and all such incidental, special and/or consequential damages are hereby also specifically disclaimed. This warranty applies only to H.S.I. equipment or materials which, after our inspection, are determined to be defective either in material supplied or workmanship performed by H.S.I. Where equipment is furnished by H.S.I. but not of its manufacture, H.S.I.’s liability is limited to such adjustment as the actual manufacturer makes to H.S.I. H.S.I. will not be liable for the cost of repairs, alterations, or replacements or any expense connected therewith made or incurred by the purchaser or his agents or employees, except upon written authority from H.S.I. This warranty is personal to purchaser only and applies only to equipment which purchaser has properly operated and maintained in accordance with H.S.I.’s written instructions. H.S.I. assumes no liability for any consequential damages suffered through the use of loss of use of its equipment. This constitutes H.S.I.’s sole warranty with respect to the equipment and material manufactured by itself. H.S.I. makes no other warranty of any kind whatsoever, expressed or implied, and all implied warranties of merchantability and fitness for a particular purpose which exceed the aforementioned obligation are hereby disclaimed by H.S.I.
11 Year Warranty
NIKOrail’s 11 year warranty is the best in the industry.
What Products Are Covered?
• Manual Workstation Enclosed Track Cranes
• Manual Enclosed Track Jib Cranes
• Defects in material and workmanship
• Wear parts (trolley and end truck wheels only)
The Fine Print:
NIKOrail by Handling Systems International, Inc. (known as NIKOrail) warrants manual push-pull Enclosed Track Workstation Crane and Jib Crane products it manufactures against defects in material or workmanship for a period of eleven years from date of receipt by purchaser or customer. This warranty is inclusive of NIKOrail crane trolley and end truck wheels. This warranty does not cover failure or defect caused by operation in excess of recommended rated capacities, misuses, negligence or accident, and alteration or repair of any kind not authorized by NIKOrail. NIKOrail systems shall not be modified after manufacture without written authorization of NIKOrail. Any field modifications made without written authorization of NIKOrail shall void all NIKOrail’s warranty obligation. NIKOrail agrees to furnish the same or substantially similar replacement part (new or repaired) free of charge,
providing the buyer gives immediate written notice of alleged defects, and if requested by NIKOrail, returns the defective parts to the factory, for NIKOrail’s inspection and examination. Purchaser or end user shall be solely responsible for all freight and transportation costs incurred in connection with any warranty work provided by NIKOrail hereunder. NIKOrail will not be liable for any loss, injury or damage to persons or property, nor for damages of any kind resulting from failure or defective operation of any materials or equipment fur-nished hereunder. NIKOrail shall not be liable under any circumstances for any incidental, special and/or consequential damages whatsoever, whether or not foreseeable, including but not limited to damages for lost profits and all such incidental, special and/or consequential damages are hereby also specifically disclaimed. This warranty applies only to NIKOrail equipment or materials which, after our inspection, are determined to be defective either in material supplied or workmanship performed by NIKOrail. Where equipment is furnished by NIKOrail but not of its manufacture, NIKOrail’s liability is limited to such adjustment as the actual manufacturer makes to NIKOrail. NIKOrail will not be liable for the cost of repairs, alterations, or replacements or any expense connected therewith made or incurred by the purchaser or his agents or employees, except upon written authority from NIKOrail. This warranty is personal to purchaser only and applies only to equipment which purchaser has properly operated and maintained in accordance with NIKOrail’s written instructions. NIKOrail assumes no liability for any consequential damages suffered through the use of loss of use of its equipment. This constitutes NIKOrail’s sole warranty with respect to the equipment and material manufactured by itself. NiKOrail makes no other warranty of any kind whatsoever, expressed or implied, and all implied warranties of merchantability and fitness for a particular purpose which exceed the aforementioned obligation are hereby disclaimed by NIKOrail.
Design Standards
All Handling Systems International Jib Cranes are structurally designed in accordance with the AISCSteel Construction Manual.
All Handling Systems International Cranes have a design factor of 15% of the allowable capacity for hoist weight and 25% of the allowable capacity for impact.
All designs meet AISC standards as they pertain to jibs and overhead cranes. All of our cranes are in accordance with OSHA specification 1910.179. All design and manufacturing is done in accordance to ANSI specification B30.11 as they apply to jib cranes and overhead cranes. All jib and gantry cranes are built to CMAA specification No. 74. All workstation bridge cranes are built to MMA MH27.2.
Fabrication Standards
All welding of Handling Systems International cranes adheres to the American Welding Society’s (AWS) standards: D1.1 for steel and D1.2 for aluminum. All welders are AWS certified.
Material Standards
All steel beams and shapes used by Handling Systems International are a minimum of ASTM A-36 designation. All steel pipes are ASTM A-53 Grade B. All steel tubing are ASTM A-500 Grade B. All aluminum used meets ASTM B308 for 6061-T6 aluminum.
Painting Procedure
All finished cranes are wire wheel cleaned and wiped down with a solvent solution paint prep to remove any standing rust, oil, or dirt that may impede in paint adhesion. Indoor and outdoor paint finishes are applied with an air-assisted wet paint sprayer. Standard indoor paint consists of a one to two coat, 2 mil +/- application with a DTM water reducible yellow enamel. Standard outdoor paint finish consists of a one coat DTM primer with two coats of water reducible safety yellow acrylic enamel.
Deflection
HSI manufactures cranes to a specific deflection value, however, the value of this formula is theoretical and will be increased during field load tests due to variables such as: installation, foundation rigidity, or the standard variation in thickness tolerances for the piping, tubing, steel plate and sheet metal. Some variation above (or below) deflections defined by the manufacturer is considered normal. When measuring deflection for safety standards, the deflection is measured at 100 percent capacity (L (span in inches)/100 for freestanding (350), L (span in inches)/150 for wall cantilever (313), free standing (351), and mast type (314), and L/450 for wall bracket (311) cranes), rather than the 125 percent load test. According to ANSI Standards (ANSI/ASME B30.2), “Standard deflection must be measured with a load of 100 percent of the rated capacity”. During load testing at 125% deflection values will thus be greater than published deflection. Using this formula, ‘L’ (meaning Length or span) measured in inches / 100, 150, or 450 will result in a theoretically calculated deflection. Load tests at 125% of rated capacity plus variables listed above can result in up to twice the theoretical deflection value.
- Inspect entire system annually or more frequently as defined by OSHA 1910.179. Inspection must be performed by a qualified person. Failure to do so may cause serious injury or death.
- This equipment, used as a crane, is not in any way designed for lifting, supporting, or transporting humans. Failure to follow specified load limitations can result in serious bodily injury or death.
- The rated load of the hoist as marked on the hoist must not exceed the rated capacity of the jib as labeled on the boom. Do not install a hoist with a capacity greater than that of the jib.
- It is solely the customer’s responsibility to provide suitable mounting supports for the jib crane. HSI recommends that the customer consult a qualified professional architect or engineer in your local area to determine the adequacy of the building support. There should be no deviation from the recommended foundation size or installation recommendations without first consulting a qualified professional. Failure to check this item can result in serious bodily injury or death.
- Do not impact end stops at speed. Only impact end stops with caution.
- Never use end stops for repetitive boom impacts.
- To prevent trolley from running off of the boom, do not operate crane without end stop bolt firmly secured in place on the end of the boom.
- Do not operate hoist or crane if cotter pins are not in place and properly bent over on both sides of hoist trolley. Check regularly that the cotter pins are in place and securing the hoist on the hoist trolley.
- Inspect jib for missing or broken parts before operating.
- Do not adjust or disassemble crane when jib is under load.
- When moving jib, position the load in the center of the boom.
- Be certain the load is directly beneath boom before load is lifted. Do not pull sideways on crane.
- Ensure the load is not attached to the floor and remove any obstacles that impede lifting.
- Adjustments and/or repairs should be made in an area where it will have the least interference with operation.
- Never stand under jib when disassembling crane.
Medium Duty Freestanding Jib Crane Model 350/350F Owner’s Manual
Tie Rod Style Jib Crane Model 311 Owner’s Manual
Cantilever Style Jib Crane Model 313 Owner’s Manual
Mast Type Style Jib Crane Model 314 Owner’s Manual
Heavy Duty Freestanding/Sleeve Mounted Jib Crane Model 351 Owner’s Manual
Heavy Duty Freestanding/Sleeve Mounted Motorized Jib Crane Model 351M Owner’s Manual
Fixed & Adjustable Steel Gantry Cranes Model 511/512 Owner’s Manual